3D 打印改變汽車行業的 9 種方式
雖然您目前還無法在經銷商處購買 3D 打印汽車,但 3D 打印多年來一直是汽車開發過程中的重要組成部分。 然而,最近,我們開始看到 3D 打印用例在整個製造過程中站穩腳跟。
3D 打印可以為供應鏈增加巨大的價值,解鎖廣泛的生產應用。 隨著公司能夠在內部採用增材製造來支持工廠車間的流程,該技術變得越來越可行和負擔得起。 新型彈性材料為生產高精度、功能性 3D 打印件提供了機會,這些打印件可以代替最終部件並提供(大規模)定制機會和高性能,但這僅僅是個開始。
用於汽車設計和原型製作的 3D 打印
原型製作歷來是汽車行業 3D 打印最常見的用例。由於使用 3D 打印進行原型製作的速度大大提高,快速原型製作實際上已成為 3D 打印的代名詞,並且該技術徹底改變了產品開發過程。
借助 3D 打印,汽車設計師可以快速製作物理零件或組件的原型,從簡單的內部元素到儀表板,甚至整車的比例模型。快速原型製作使公司能夠將想法轉化為令人信服的概念證明。然後可以將這些概念推進到與最終結果非常匹配的高保真原型,並最終引導產品通過一系列驗證階段走向大規模生產。
由於產品要經歷多次迭代,原型製作過去既費時又費錢。借助 3D 打印,可以在一天內創建具有高度說服力、代表性和功能性的原型,成本遠低於傳統製造方法。桌面 3D 打印機允許工程和設計團隊將技術引入內部,以增加迭代周期並縮短創意與最終產品之間的距離,從而加強他們的整體產品開發工作流程。
- 使用 3D 打印的當天汽車原型
在德國 Merkenich 的福特快速技術中心,許多 3D 打印技術用於創建原型,周轉時間短。工程師和設計師無需將工作發送到需要幾週交貨時間的商店,而是能夠在幾小時內將他們的設計掌握在手中。
設計人員能夠在快速技術中心製作當日原型,在短短幾個小時內多次修改設計。福特增材製造專家 Bruno Alves 表示,3D打印的物產品原型可以提供優於數字模型的優勢。
例如,Formlabs 3D 打印機被用於製作福特 Puma 背面的字母原型,讓設計師能看到線條和陰影在不同光照條件下的呈現方式。 “對於這種字體,打印機速度如此之快,效果如此之好,以至於我們可以為設計師提供迭代的機會,”Alves 說。 “這是一種你可以在 CATIA 或其他軟件中看到的東西,你可以模擬照明,但當你把字貼在汽車上時,感覺、觸摸和看到所有反射都是不同的。”
2. 使用 3D 打印輕量化汽車零件
IGESTEK 是西班牙的一家汽車供應商,專注於使用塑料和復合材料開發輕量化解決方案。他們的團隊在整個產品開發過程中使用 3D 打印,從驗證幾何形狀的概念設計階段到實現功能原型的詳細設計階段。他們還使用 3D 打印來製造快速模具,例如用於塑料注射模具的嵌件或用於復合材料的熱成型工具。
拓撲優化是輕量化領域的熱門話題。 IGESTEK 使用 Autodesk Fusion 360 根據參數列表生成多個解決方案。
對於一個懸架,該團隊開發了一種多材料架構,該架構結合了基於生成幾何形狀的金屬 3D 打印和更輕的複合材料,以提供最佳性能,包裝比市場上現有的解決方案輕 40%。這些零件是在 Form 3L 上製作原型的,該 Form 3L 足夠大,可以同時製作多個設計的原型,以實現更快的迭代和測試。
- 通過 3D 打印讓概念車栩栩如生
Vital Auto 是英國的一家工業設計工作室,與沃爾沃、日產、蓮花、邁凱輪、吉利、TATA 等主要汽車品牌合作。當原始設備製造商 (OEM) 自己沒有時間進行實驗時,他們會來 Vital 將想法、初始草圖、圖紙或技術規格轉化為完全實現的物理形式。
“我們從第一天起就使用 3D 打印。我們想將它引入我們的製造流程,不僅是為了降低成本,也是為了讓客戶的設計和想法更加多樣化,”負責增材製造的設計工程師 Anthony Barnicott 說。
如今,Barnicott 經營著一個完整的 3D 打印部門,包括 14 台大幅面熔融沈積建模 (FDM) 打印機、三台 Formlabs Form 3L 大幅面立體光刻 (SLA) 3D 打印機和五台 Fuse 1 選擇性激光燒結 (SLS) 3D 打印機。 “就產能而言,幾乎從第一天開始,所有這些打印機都以 100%、24/7 的速度運行。我們將這些打印機用於我們概念和設計的所有領域。通常,我們將 Fuse 1 用於基於生產的零件,將 Form 3L 用於基於概念的零件,”Barnicott 說。
3D打印不僅可以幫助團隊更快地創造出更好的產品,還可以吸引新的業務。他們發現他們的許多客戶求助於他們,因為他們希望獲得最新技術,並且希望使用最新的尖端材料製造組件。
“過去 10 年技術和 3D 打印的進步是驚人的。當我剛開始生產小批量、小眾汽車時,我們今天生產的一些產品根本無法獲得。我現在不僅能夠生產這些零件,而且還能非常經濟高效地生產它們,”Barnicott 說。
汽車製造中的 3D 打印
由於3D打印機和高性能材料的快速發展,增材製造現在可以用於生產能夠應對極端環境挑戰的零件。
3D 打印可用於製造,通過定制夾具和夾具等製造輔助工具降低開銷並提高效率,並為註塑成型或熱成型等傳統製造工藝生產小批量快速模具。
3D 打印的最終用途部件在汽車行業也越來越普遍,特別是對於售後市場、定製或更換部件等應用,在這些應用中,其他生產方式成本過高且速度過慢。
4. 汽車零件的 3D 打印模具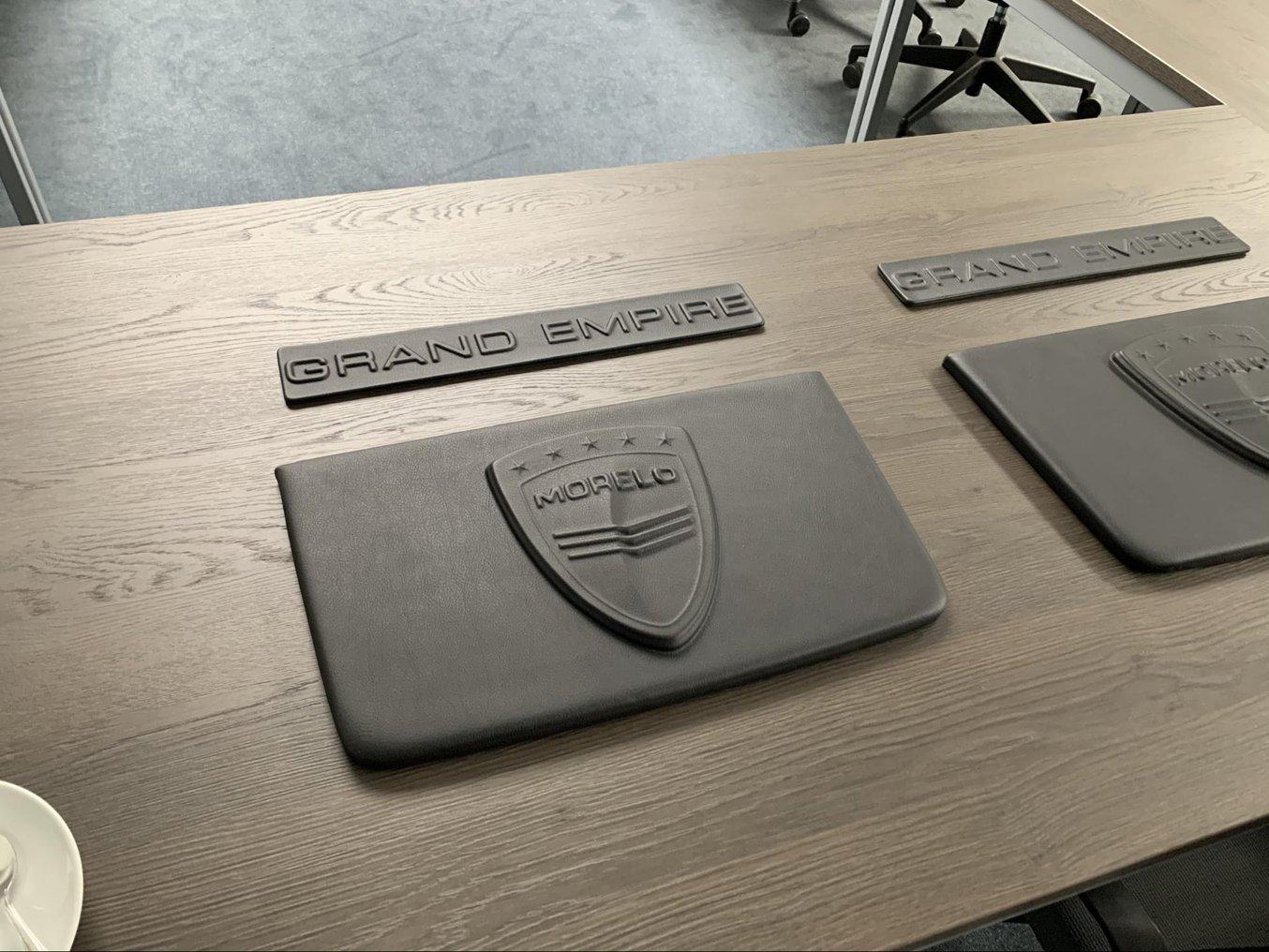
Makra Pro 是一家增材製造服務提供商,開發了一種使用 3D 打印模具成型皮革的新工藝,皮革是一種在豪華汽車中流行的裝飾材料,很難成型。他們與一些客戶(包括豪華汽車、摩托車和房車製造商)合作,測試了一種真皮塑形和壓花方法。
Makra Pro 的技術使用印在 Form 3 上的模具,使用膨脹的泡沫在拉伸皮革面板上平均分配壓力。隨著泡沫變硬,皮革被壓入模具並成形。
完成後的皮革部件可以,例如,在汽車的門板上拉伸或連接到車輛的座套上。一家知名的限量版豪華汽車改裝公司將這些模製皮革部件用於車輛增強的牆壁或天花板。
- 3D 打印製造輔助工具
Dorman Products 為數百種不同的車輛設計和管理一個包含超過 100,000 個零件的數據庫。 “從歷史上看,我們每年發布 4,000 到 5,000 個新零件,”機械設計團隊經理 Eric Tryson 說。
增材製造負責人 Chris Allebach 表示,除了作為售後市場供應商運營的純粹後勤挑戰外,Dorman 的產品設計和製造團隊還需要特別敏捷。 “原始設備製造商擁有設計單個零件的團隊,有時在新車問世前兩年就開始設計。我們需要找到方法來確保我們的替代品可靠,同時又能快速推向市場。”
在將 3D 打印機集成到他們的工作流程之前,缺乏定制測試夾具是快速開發的障礙。機加工非常昂貴且耗時。
“現在,借助 3D 打印機,我們開發了測試夾具和儀表以及產品原型,因此當我們決定最終設計時,我們也可以使用夾具對其進行測試。我們正努力盡可能主動,”Allebach 說。
自從 Dorman 十年前購買了他們的第一台 3D 打印機以來,Allebach 和 Tryson 穩步增加了更多的打印機,不斷地最大化他們現有設備的容量,並在他們的 Formlabs SLA 打印機上使用完整的材料庫,包括大幅面 Form 3L。
“[我們的第一台 3D 打印機] 在兩個月內就收回了成本。當我們為任何 Formlabs 打印機進行成本論證或投資回報率時,我們可以在幾個月而不是兩年的時間框架內證明回報的合理性。這讓我們的領導層相信 3D 打印是一項值得的投資,”Tryson 說。
Dorman Products 正在將 3D 打印用於其他幾個應用。閱讀我們的文章來探索它們。
- 最終使用 3D 打印的售後零件
與許多成功的企業一樣,BTI Gauges是從市場空白開始的。 Brandon Talkmitt,創始人兼所有者,正在為他的高性能汽車尋找一種可定制的遙測顯示方法。
Talkmitt 搜索了一個包含多個性能指標的儀表,但沒有成功,因此他的擋風玻璃上沒有散落著多個屏幕和分散注意力的讀數。然後,他開始在 3D 打印機上製作儀表外殼的原型並親自進行測試,將外殼置於汽車和烤箱內的高溫環境中,並修改設計以補充多種車型。
立即,駕駛 1990 年代風格的日本賽車、蘭博基尼、道奇毒蛇和其他高性能車輛的客戶對他的產品產生了興趣。
Talkmitt 開始評估其他 3D 打印選項,包括昂貴的塑料粉末床融合 3D 打印機、樹脂 3D 打印機和便宜的緊湊型 SLS 選項。但在一些 50 萬美元的價格標籤和其他復雜的材料採購過程之間,沒有任何選擇。直到他聽說了 Fuse 1。“當我拿到樣品時,我想,‘伙計,如果我的零件能看起來像這樣的話。’所以我進行了一些測試,弄清楚它能承受什麼樣的熱量。對它進行了精加工和噴漆過程,一切正常,”Talkmitt 說。
在過去兩年的供應鏈問題中,BTI Gauges 面臨觸摸屏顯示器和九個產品線所需的其他組件的多次短缺。通過在內部使用 Fuse 1 進行 3D 打印,他能夠立即轉向新設計,而無需花費數千美元購買新工具,也不必處理積壓的現已過時的產品。
“我會被所有塑料所困,但有了 Fuse 1,我可以即時做出改變。更改文件對我來說是 30 分鐘的事情。沒有它,我現在肯定會被困住,”Talkmitt 說。
在我們與 BTI 儀表的深度報導中,了解有關生產最終用途售後市場零件的更多信息。
用於賽車和摩托車的 3D 打印
3D 打印是一種無需工具的製造工藝,非常適合賽車運動,是快速且經濟高效地實現小批量生產和定制製造的強大工具。 通過消除工具時間和成本,它提供了快速修改產品和加快上市時間的靈活性。 它增加了設計自由度,並提供了定制產品和構建複雜形狀(如格子)的能力,而無需任何額外成本。
通過使用內部 3D 打印,賽車運動團隊可以更快地開發、保護其 IP 安全、測試更多創意並最終擊敗競爭對手。
- 通過 3D 打印迭代設計提高發動機性能
Forge Motorsport 為高性能汽車製造售後零件,使用 3D 打印來製作零件原型。當 Toyota Yaris GR 發佈時,Forge 的工程師注意到一些改進進氣道設計的機會——移動空氣箱開口,並增加零件的整體尺寸——這將減少進氣溫度 (IAT) 的波動,這很難預測發動機性能,同時降低整體平均溫度。
他們使用 3D 掃描對 OEM 零件進行逆向工程,並在 SOLIDWORKS 中虛擬地進行設計更改,他們能夠在其中模擬氣流。一旦他們有了一個可行的 3D 模型,他們就會在快速打印的 Draft Resin 中製作原型,他們用它來確認空氣箱開口的新位置可以按預期工作,並且零件的整體尺寸增加不會干擾其他組件或電纜。確認基本適合後,他們使用堅固且抗衝擊的材料 Tough 1500 Resin 重新打印零件,將其塗成黑色以類似於最終零件,並將其交給客戶進行測試。
客戶在他的 Yaris GR 中使用 3D 打印部件五個月,在此期間他收集了不同條件下的性能數據,包括賽道和上坡。備用部件的 IAT 在 42-45 °C 之間變化,在比賽過程中觀察到相當大的變化;對於重新設計的部件,使用 Tough 1500 樹脂印刷,客戶測得 IAT 在 35-36 °C 之間。正如預期的那樣,重新設計的部件具有更低的整體 IAT 和更低的波動。有了這些數據,Forge 確信他們的零件是對 OEM 設計的改進,因此開始使用碳纖維製造最終生產零件。
- 方程式賽車的碳纖維成型和 3D 打印最終部件
Formula Student 是一年一度的工程設計競賽,來自世界各地的學生團隊會建造和競賽方程式賽車。柏林工業大學大學生方程式賽車隊 (FaSTTUBe) 是最大的團體之一;自 2005 年以來,每年都有 80 到 90 名學生開發新的賽車。該團隊在他們的工具集中添加了 Form 3 SLA 3D 打印機,他們用它來節省時間、降低成本,並製造碳纖維零件,這些零件在任何其他地方都非常昂貴方法。
複合材料的 3D 打印模具使團隊在設計方向盤底盤等關鍵部件時具有更大的靈活性、更短的交貨時間並節省了成本。加工該零件的模具需要採購昂貴的專用工具,而外包成型零件則需要數週時間並花費近 1000 歐元。相反,內部 3D 打印模具並手工層壓僅需 10 歐元的材料成本和 1.5 小時的工作時間。
該團隊還使用 3D 打印來製作原型設計、輕量化部件,甚至製造最終用途部件。閱讀我們與他們的故事,了解有關這些應用程序的更多詳細信息。
3D 打印為 FaSTTUBe 團隊帶來了新的靈活性、設計自由度和成本節約。此外,學生還獲得了為他們的項目製造原型、工具甚至最終用途部件的經驗。這些技能將在學生進入勞動力市場時一直伴隨著他們,為每個工程學科帶來寶貴的經驗。
- Andrea Pirazzini 自 2012 年以來一直騎摩托車。他想挑戰自己,為自己的自行車設計和製造功能強大、安全的 3D 打印進氣歧管。過去,他曾嘗試使用 FDM 打印技術,但結果並不如他所願,因為零件不密封,影響了發動機的功能。
為開發該項目,Pirazzini 使用 3D 掃描和 Autodesk Fusion 360 軟件對設計進行逆向工程。對四衝程發動機(雙氣門)發動機及其框架和化油器的掃描幫助他正確確定了歧管的尺寸,然後將其放置在最佳位置。通過使用 CAD 軟件,可以將汽缸頭入口的直徑與化油器對齊,避免台階和任何壓降或湍流。
新的歧管設計是使用 Form 3 使用剛性 10K 樹脂以 100 微米的層高打印的,形成了光滑的表面,沒有可見的層線。至於表面處理,Pirazzini 使用經典的水性砂紙打磨表面。與必須在外部和內部進行防水處理的 FDM 歧管不同,SLA 打印可創建堅固且防水的部件。
Pirazzini 用 Form 3 打印的歧管完美地承受了高溫和低溫,並且仍然安裝在他的越野車上。由於使用熱像儀,Pirazzini 發現剛性 10K 樹脂還提供了明顯更好的熱性能:與傳統的鋁製歧管相比,帶有散熱片的 3D 打印歧管記錄的溫度低 40-50 攝氏度。此外,在大約 33 攝氏度的外部溫度下進行了大約 20-25 分鐘的比賽后,可以觸摸歧管而不會被燙傷。
該項目不僅成功了,而且還改進了引擎的功能。基於 Pirazzini 對原始設計所做的一些改進,與標準機加工歧管相比,該發動機具有更大的馬力(約 1 HP,增加近 10%),同時保持在錦標賽規則規定的限制範圍內。